Today I was out of the water and back on dry land in the Boisbuchet workshops. As Day 3 begins and the presentation of our object is looming, I started early fro Friday is the day after next. I further tested methods of ‘cold joining’ discovering some beautiful connections formed with tapered chisels and even the humble workshop vice. The Vice performed as a press, a hammer, and a texture maker. Pressings and twists acted like rivets interlocking elements to form a new aesthetic and joining method.
Other methods of joining where explored with the last test for the day being a pice of PVC tube being squeezed and twisted. A sample was made with timber and copper and real design magic happens.
Things are really being stretched in all directions and my ideas are like a hose filling a swimming pool on a hot French summers day – It just can’t happen quickly enough.
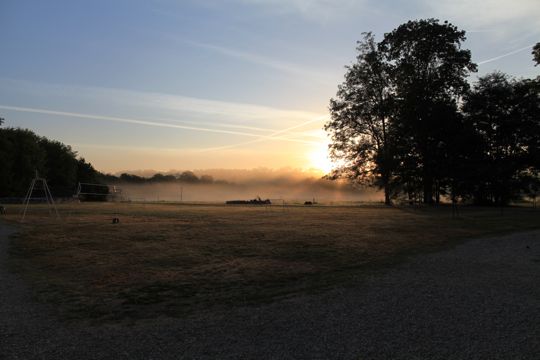
The day started early in the south of France – Looking across the grounds of Domaine de Boisbuchet – Tomas Kral Boisbuchet – Image Dean Homicki
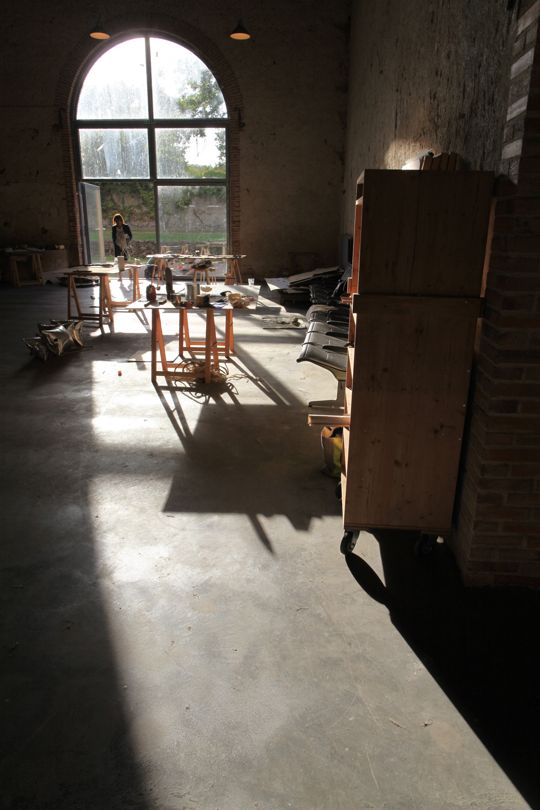
I got up early before the designer stampede began – Inside the main hall/barn of Domaine de Boisbuchet – Tomas Kral Boisbuchet – Image Dean Homicki
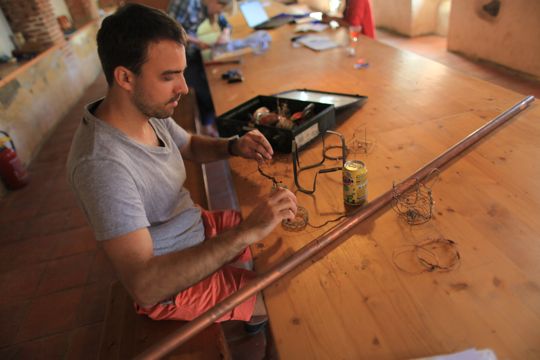
‘Tomas Kral reviewing yesterday’s work and research tests’ – Tomas Kral Boisbuchet – Image Dean Homicki
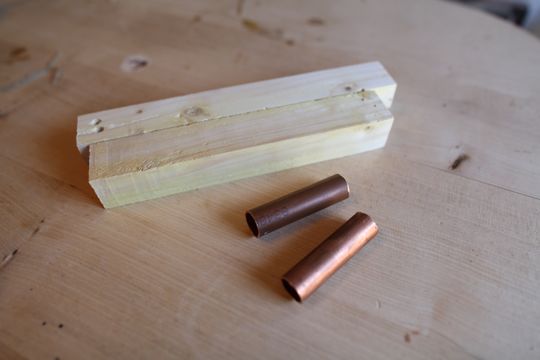
‘I further tested methods of cold joining. Pine and Copper tube’ – Tomas Kral Boisbuchet – Image Dean Homicki
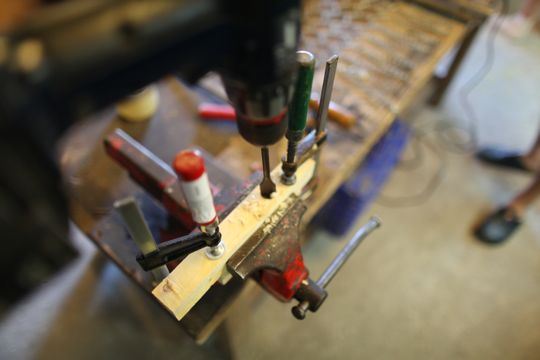
‘The timber is clamped ready to create test holes that will receive the copper tube’ – Tomas Kral Boisbuchet – Image Dean Homicki
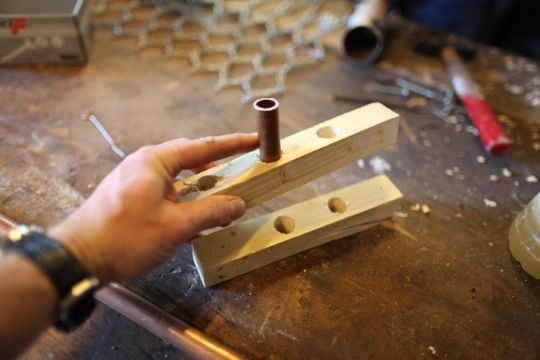
‘Copper tube, cut to the combined width of the pieces of Pine, are inserted into the drilled holes’ – Tomas Kral Boisbuchet – Image Dean Homicki
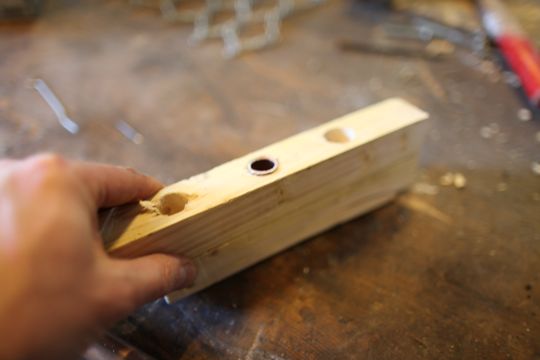
‘The Copper tube is made flush with the outer surface of the Pine’ – Tomas Kral Boisbuchet – Image Dean Homicki
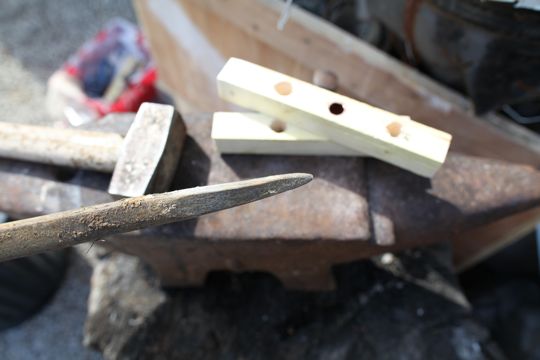
‘Using what was available, this steel bar was used to swage the Copper tube inserted into the timber’ – Tomas Kral Boisbuchet – Image Dean Homicki
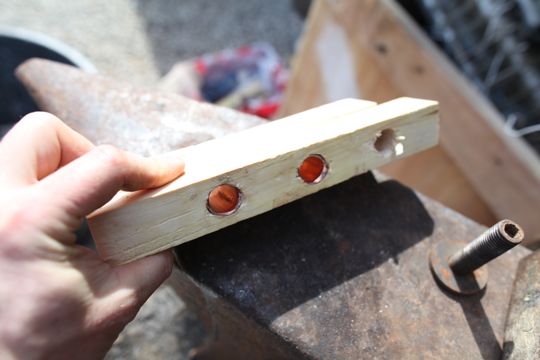
‘The second Copper tube is inserted and swagging is repeated on both sides on the pine pieces’ – Tomas Kral Boisbuchet – Image Dean Homicki
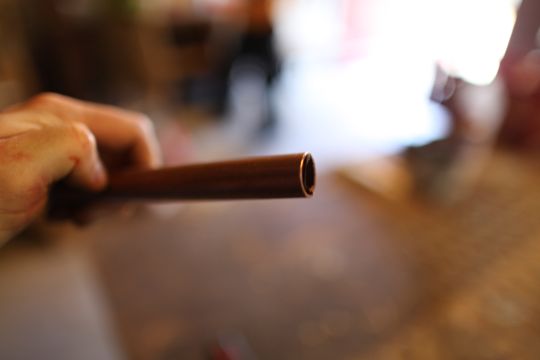
‘What else could we use the copper for? What about using the Copper tube as a crimp rather than a rivet? What tool could make this?’ – Tomas Kral Boisbuchet – Image Dean Homicki
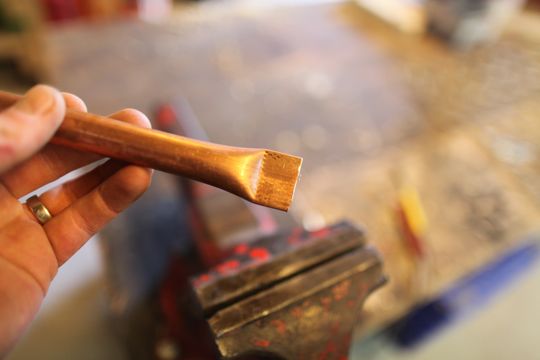
‘Looking good. The vice ‘Tool’ is leaving impressions from the jaws on the surface of the Copper’ – Tomas Kral Boisbuchet – Image Dean Homicki
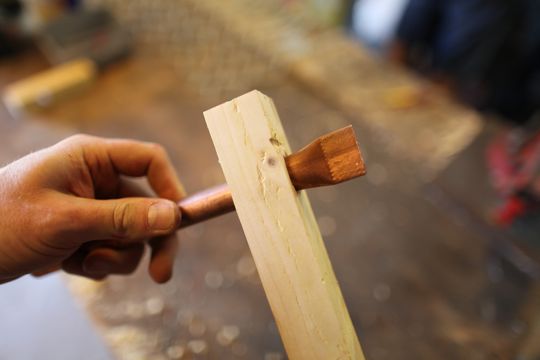
‘The crimped Copper tube is inserted through a pre-drilled hole in Pine’ – Tomas Kral Boisbuchet – Image Dean Homicki
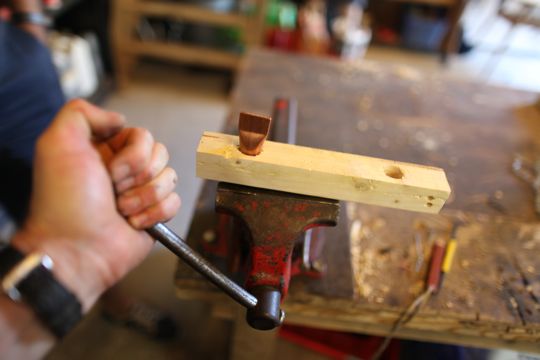
‘The crimp acts as a ‘Rivert Head’ and allows for a second ‘Locking Crimp’ on the opposite side. This creates a Rivet’ – Tomas Kral Boisbuchet – Image Dean Homicki
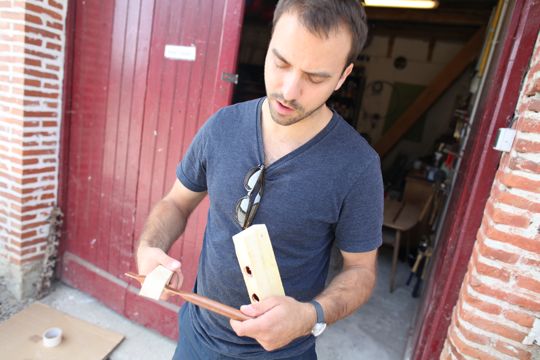
“This is interesting Dean – Your tool is now a vice” Tomas Kral inspects one of the several test samples created – Tomas Kral Boisbuchet – Image Dean Homicki
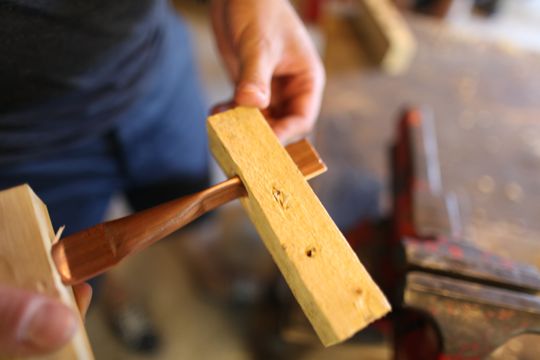
”The Vice performed as a press, a hammer, and a texture maker. Pressing and twists acted like rivets interlocking elements to form a new aesthetic and joining method’ – Tomas Kral Boisbuchet – Image Dean Homicki
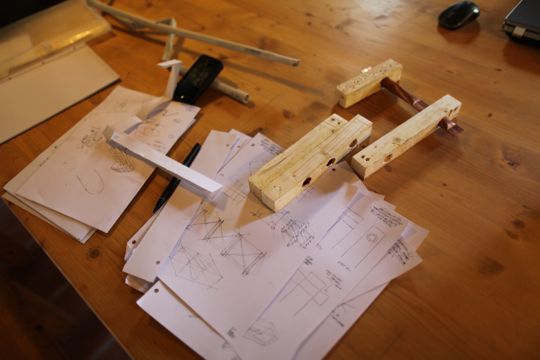
‘It’s time to design a second product from this newly discovered tool. Time to draw’ – Tomas Kral Boisbuchet – Image Dean Homicki
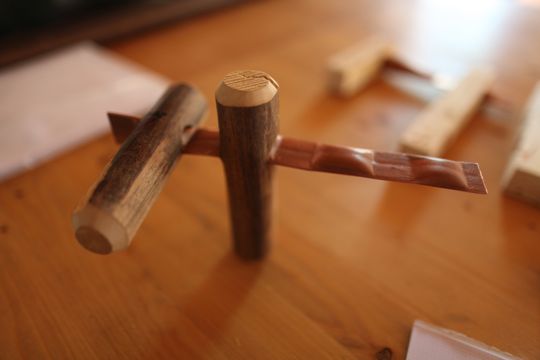
‘After drawings and further discussions with Tomas Kral, A stool design was conceived. Yet another sample showing the connection and joining section is created’ – Tomas Kral Boisbuchet – Image Dean Homicki
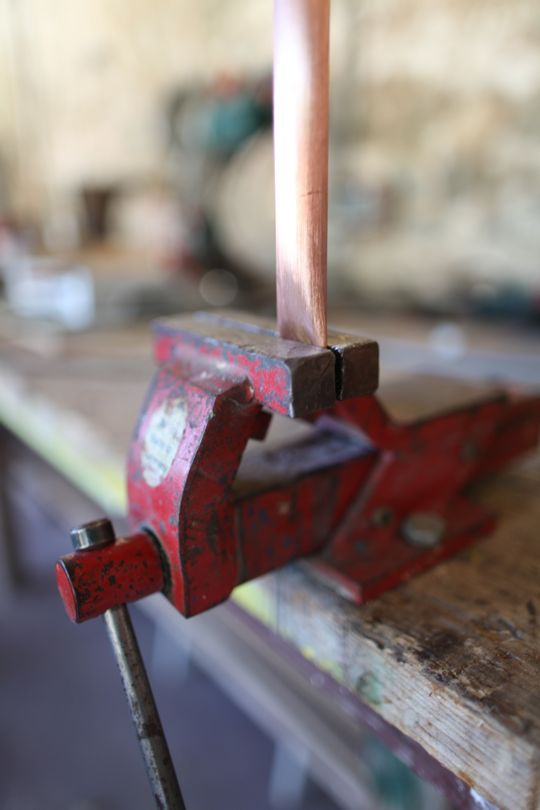
‘Additional Pressings and twists are tested. This is the start of the ribs that will become the seat’ -
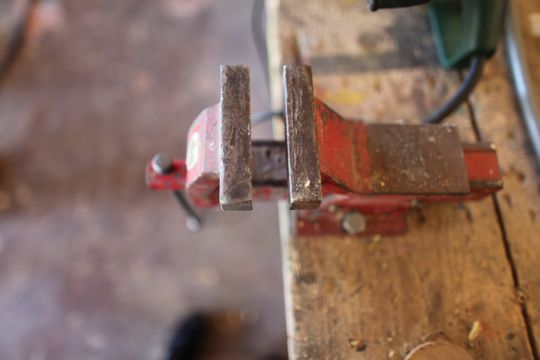
‘Oh yeah, this is the humble vice. A long way from additive manufacturing’ – Tomas Kral Boisbuchet – Image Dean Homicki
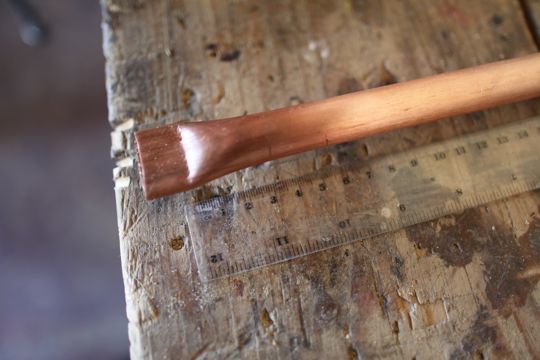
‘With the first crimp complete, a spacing for additional crimping is considered’ – Tomas Kral Boisbuchet – Image Dean Homicki
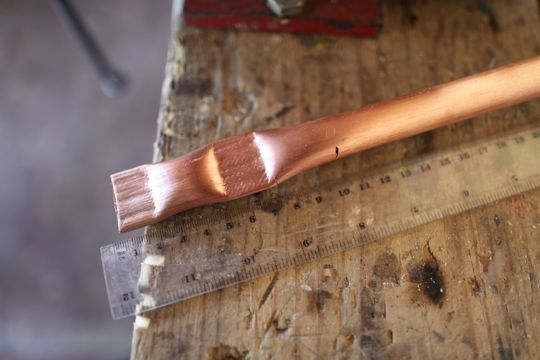
‘A second crimp is formed by the vice and an additional spacing metric is calculated’ – Tomas Kral Boisbuchet – Image Dean Homicki
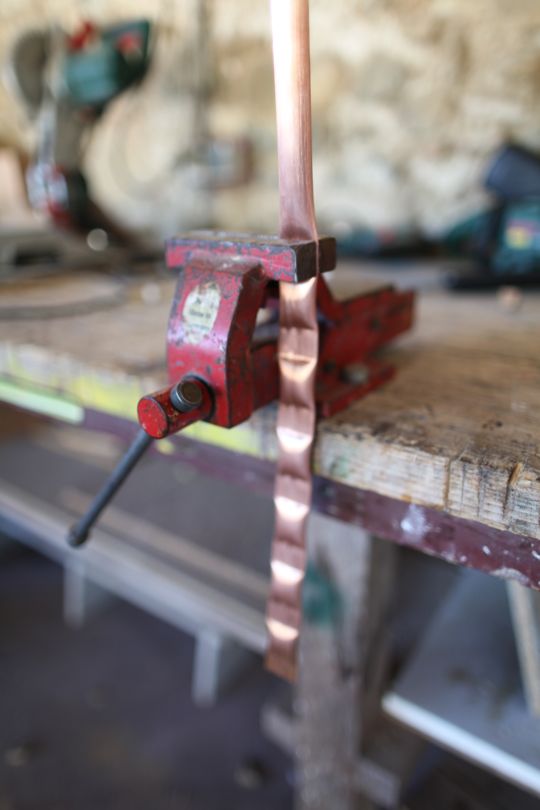
‘A unique quality of tool, process and material is developing through repetative pressings’ – Tomas Kral Boisbuchet – Image Dean Homicki
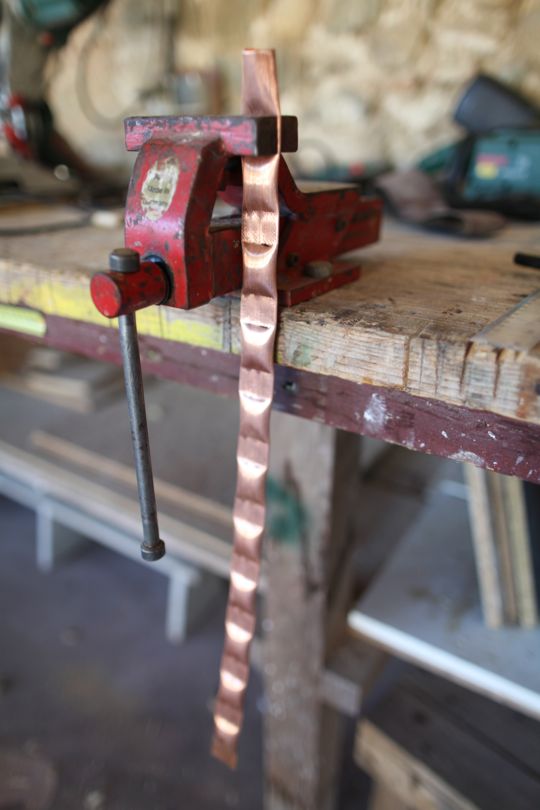
‘The crimping is tested for distortion and material stress of the Copper’ – Tomas Kral Boisbuchet – Image Dean Homicki
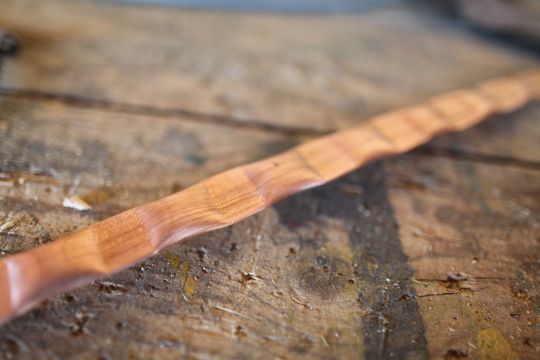
‘An amazing discovery and a pleasing result. The Copper tube has become a rope of pillows’ – Tomas Kral Boisbuchet – Image Dean Homicki
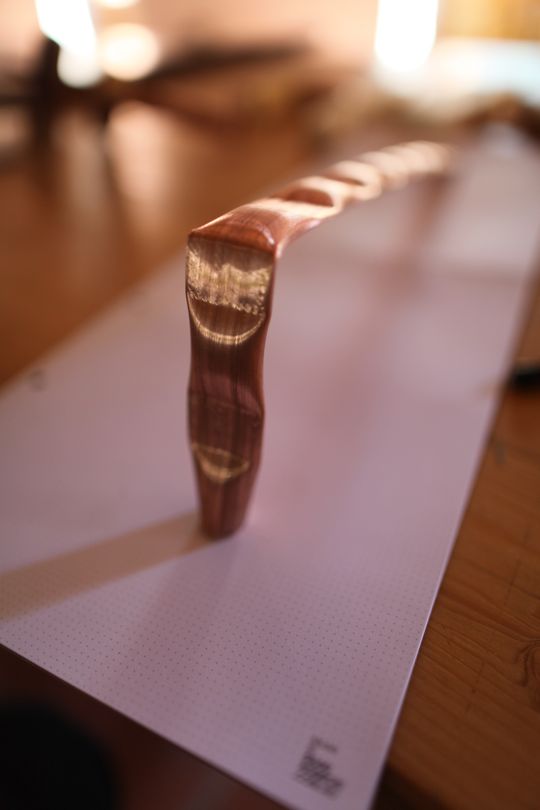
‘Testing of additional bends for what will become the seat strips of the stool’ – Tomas Kral Boisbuchet – Image Dean Homicki
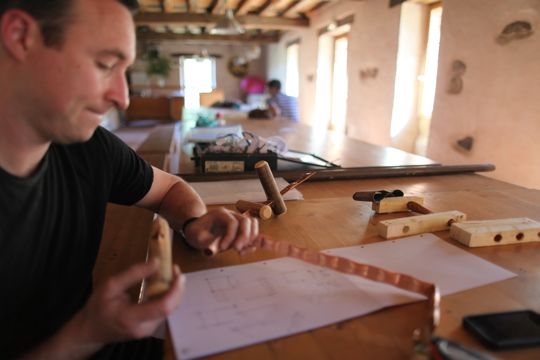
‘FInal design modifications are considered. This is what the vice made…’ – Tomas Kral Boisbuchet – Image Dean Homicki
This document – ‘DAY 3 – MADE BY VICE – DOMAINE de BOISBUCHET France’ is authored by Dean Homicki. It is free to copy, use and alter providing attribution and reference to deanhomicki.com.au is noted. ‘DAY 3 – MADE BY VICE-DOMAINE de BOISBUCHET France’ – Dean Homicki – Designer, Entrepreneur, Mentor