Starting with P.V.C. tube and copper tests from DAY 3 – ‘MADE BY VICE – , the vice was trailed by clamping the copper at regular intervals. Intrinsically, pillow like bubble shapes appeared. Like lollies being sealed in plastic packaging on a conveyor belt, the copper takes on a unique, soft, ‘try and eat me quality’. Not that you would try?.
The researched linked back to DAY 2 – ‘MADE BY WATER’ object with almost a lattice like resemblance occurring. Old garden tool handles were cut and fashioned into braces (timber cross members) and the elements found themselves becoming a stool. This was a good vice to be in and being squeezed, as I was under the influence of Tomas Kral and Paloma Canizares of PCM, the object began continuing to announce its own distinct identity. It’s been a long day and I worked late into the night. Tomorrow is presentation day.
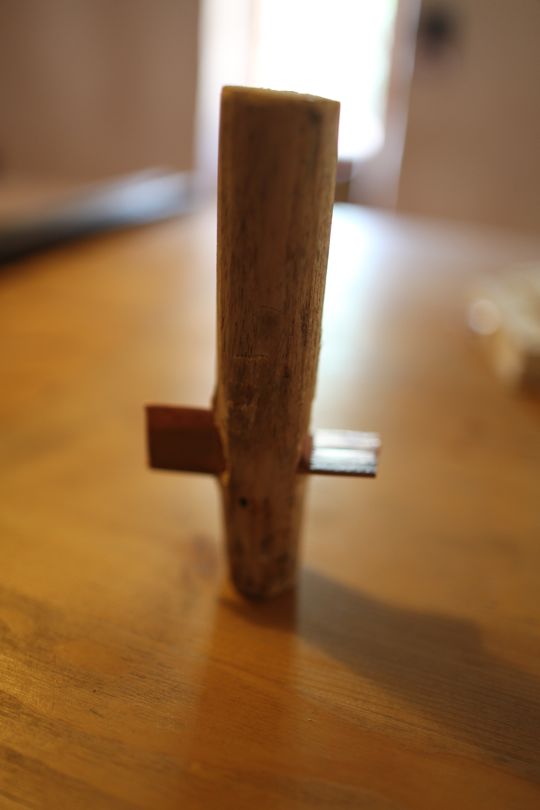
‘The final section and sample for the stool, the completed 2nd object of the workshop will be made today.’ – Tomas Kral Boisbuchet – Image Dean Homicki
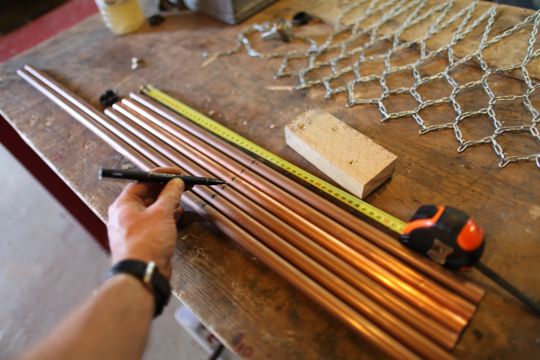
‘The copper is cut to size from the schema devised to make the stool – A center line is found as we will work from the inside to the outer edge of each copper tube’ – Tomas Kral Boisbuchet – Image Dean Homicki
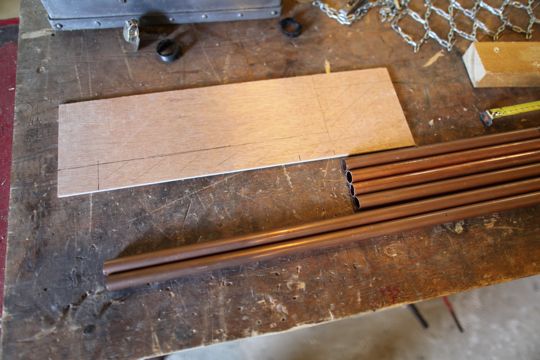
‘To make the measuring simple and accurate, a positioning template is drawn up and made.’ – Tomas Kral Boisbuchet – Image Dean Homicki
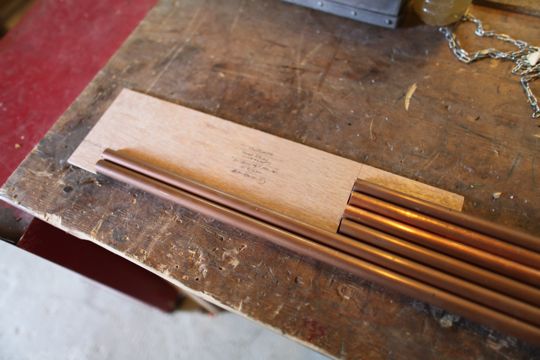
‘The new template now make measuring fast and easy helping to all the copper tube segaments’ – Tomas Kral Boisbuchet – Image Dean Homicki
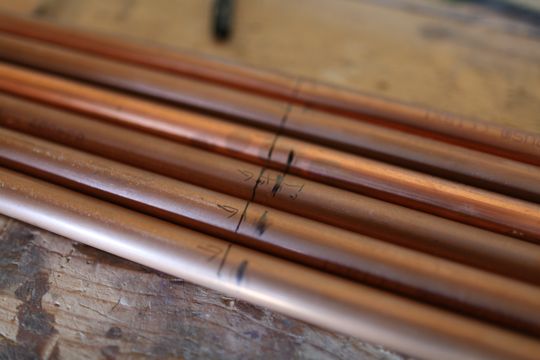
‘The first marks are made on the copper making them ready to be crimped by the vice’ – Tomas Kral Boisbuchet – Image Dean Homicki
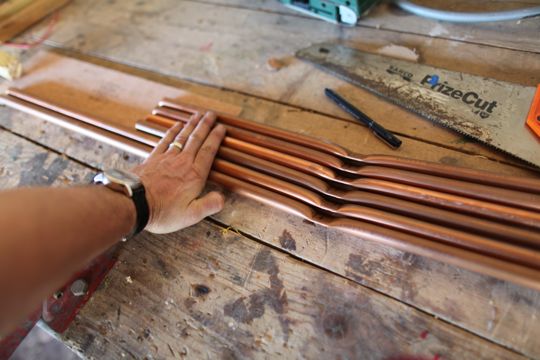
‘The first centre crimp is made on all the copper segments. The parts are the inserted back into the template for the remaining measurement marks’ – Tomas Kral Boisbuchet – Image Dean Homicki
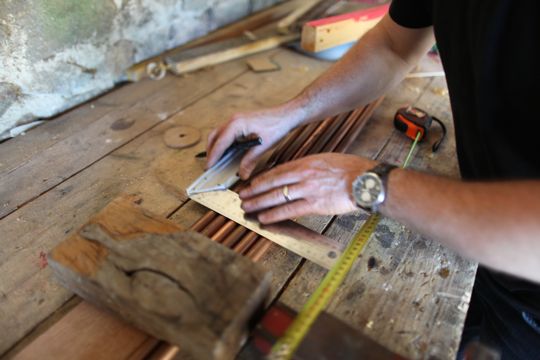
‘A carpenters square is used to make all the measurements across all parts in one go.’ – Tomas Kral Boisbuchet – Image Dean Homicki
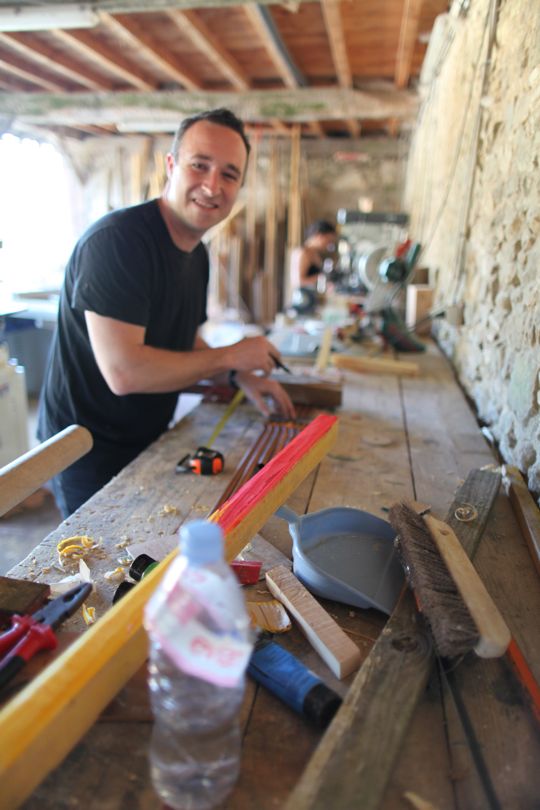
‘This is a lt of fun..and a quick pic to remember just how much’ – Tomas Kral Boisbuchet – Image Anna Phillips
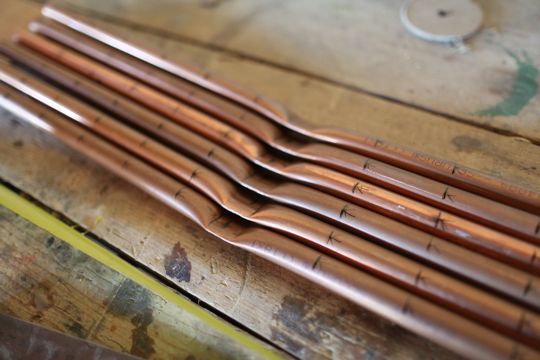
‘All marking for the crimping is complete. Ready to crimp the copper tube in the vice’ – Tomas Kral Boisbuchet – Image Dean Homicki
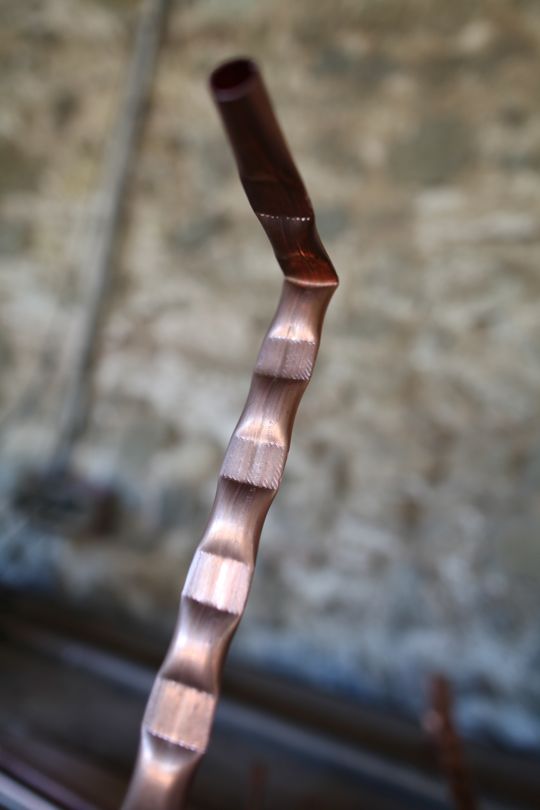
‘A 90 degree bend is made one copper bubble up from each end. This will eventually be inserted and clamped by timber cross members’ – Tomas Kral Boisbuchet – Image Dean Homicki
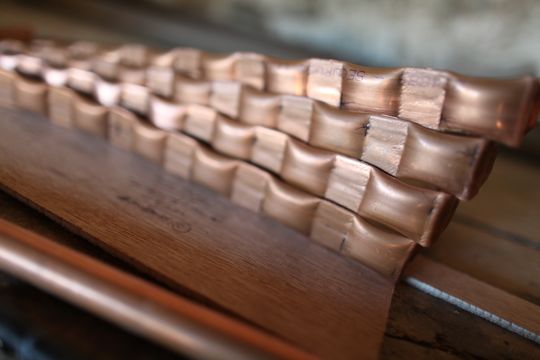
‘Completed copper tube bubble segments ready for assembly’ – Tomas Kral Boisbuchet – Image Dean Homicki
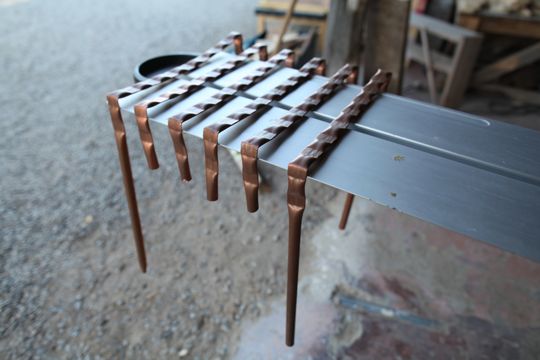
‘Taking shape. The copper segments are loosely positioned for review.’ – Tomas Kral Boisbuchet – Image Dean Homicki
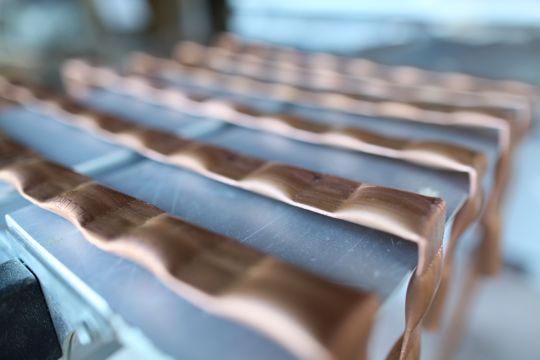
‘Close up of the complete ‘made by vice’ copper segments. The design is truly formed by it inherent process’ – Tomas Kral Boisbuchet – Image Dean Homicki
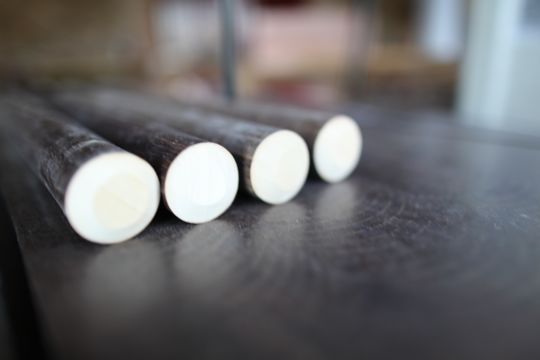
‘Time to make the timber cross members. Old Garden tool handles are salvaged from the workshop stores – Thank you Alessandro.’ – Tomas Kral Boisbuchet – Image Dean Homicki
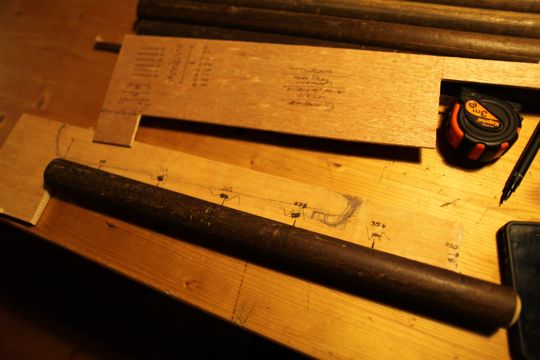
‘Another template is devised, this time to mark the position of the holes in teh timbers cross members that will take the completed copper tubes .’ – Tomas Kral Boisbuchet – Image Dean Homicki
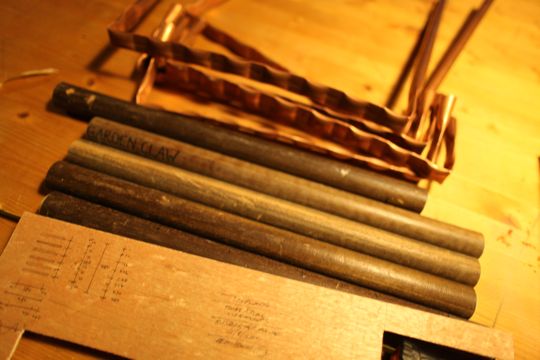
‘Final checks are made for the measurements – There is no more timber or copper available in the workshops – No room for error.’ – Tomas Kral Boisbuchet – Image Dean Homicki
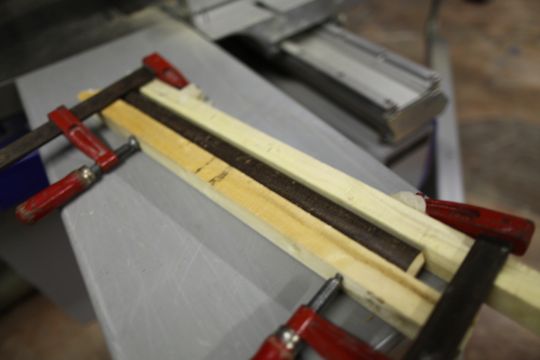
‘The timber cross member are clamping in timber ready for drilling holes – Tomas Kral Boisbuchet – Image Dean Homicki
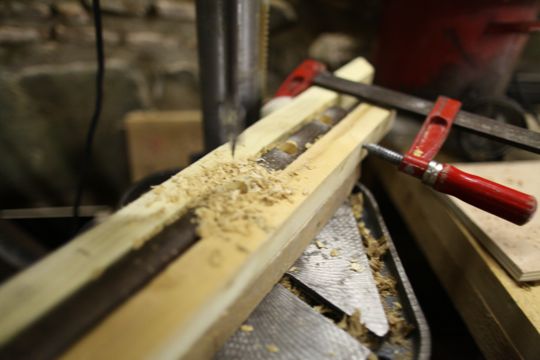
‘The holes are drilled using a drill press – (Many thanks to the industrious designer marionchatel.com who allowed me to use her tool ‘The drill press’ late in the night before presentation day…you are very kind’ – Tomas Kral Boisbuchet – Image Dean Homicki
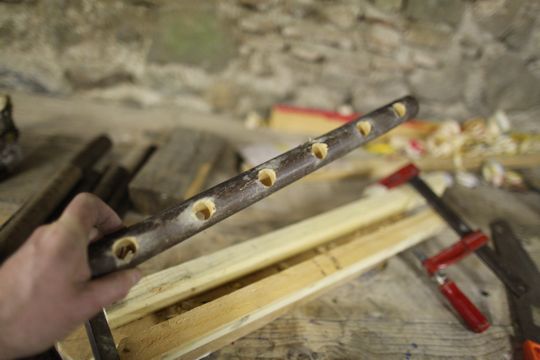
‘A timber cross member is release from the clamp device used for drilling the holes accurately. Now sanding is required to complete the finishing of the parts’ – Tomas Kral Boisbuchet – Image Dean Homicki
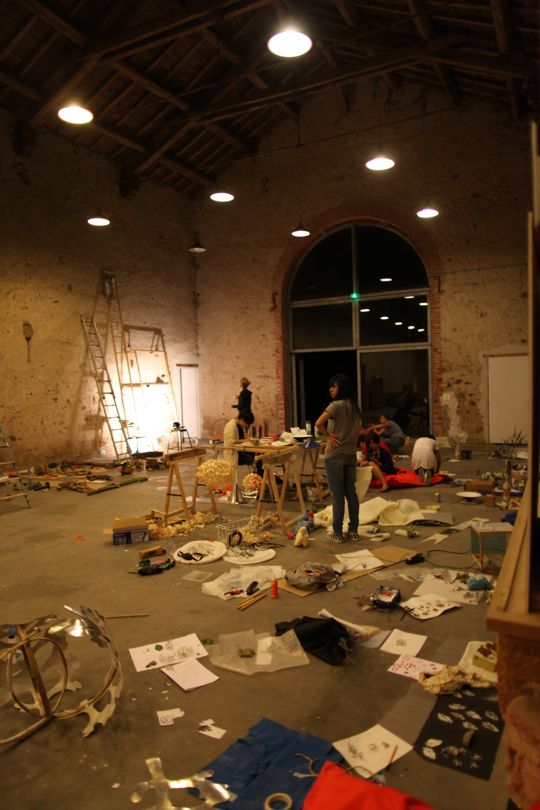
‘A quick pic of other designers slaving it out late into the night inside the hall/barn of Domaine de Boisbuchet. That is not mess. It is transformative assembly!’ – Tomas Kral Boisbuchet – Image Dean Homicki
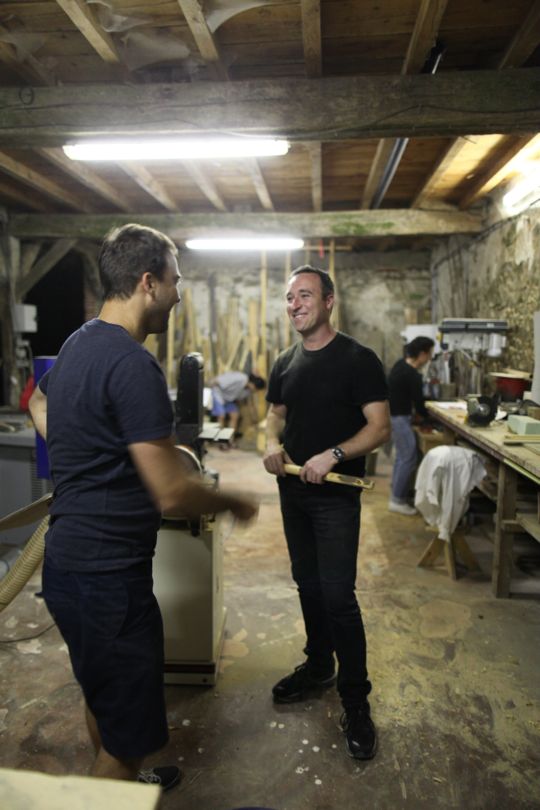
‘Tomas Kral comes to inspect and keep our spirits high. Tomas worked very hard with all the participants in his workshop. Thanks mate!’ – Tomas Kral Boisbuchet – Image Dean Homicki
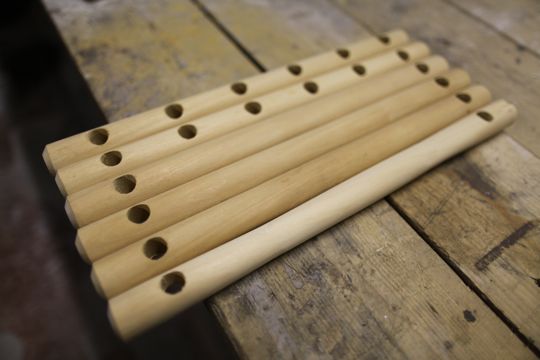
‘With all the timber cross members sanded and complete only assembly with the copper segments is required – Tomas Kral Boisbuchet – Image Dean Homicki
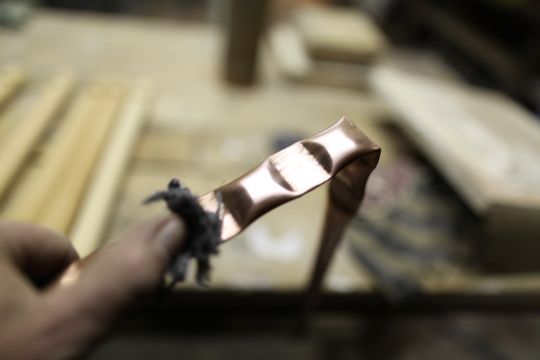
‘Final details. The copper bubble segments are rubbed with vinegar and steel wool for a crisp satin sheen’ – Tomas Kral Boisbuchet – Image Dean Homicki
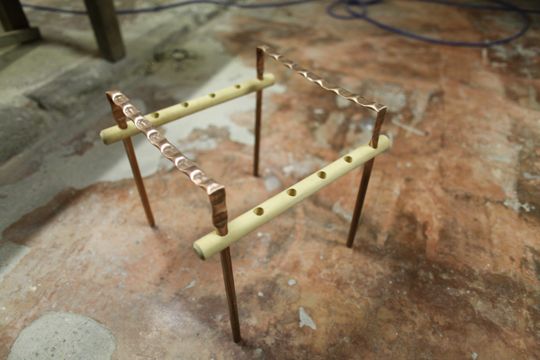
‘The stool begin to emerge. The outer legs are assembled first held in position by a pair of timber cross members’ – Tomas Kral Boisbuchet – Image Dean Homicki
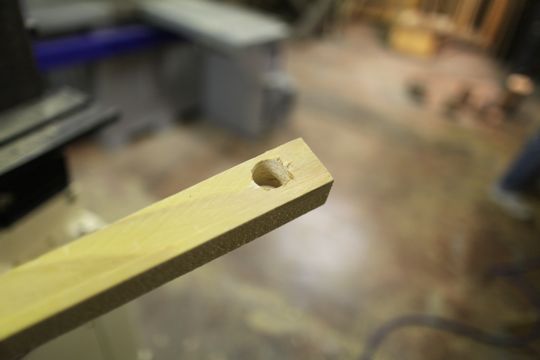
‘A quick wooden press device was formed to squeeze the timber cross members against the last copper crimp on each leg segment’ – Tomas Kral Boisbuchet – Image Dean Homicki
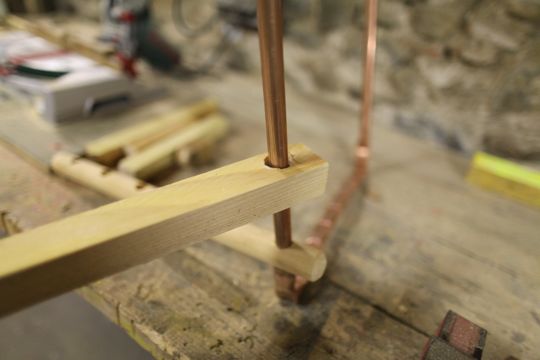
‘The timber cross members are gentle forged against the last copper crimp on each leg segment’ – Tomas Kral Boisbuchet – Image Dean Homicki
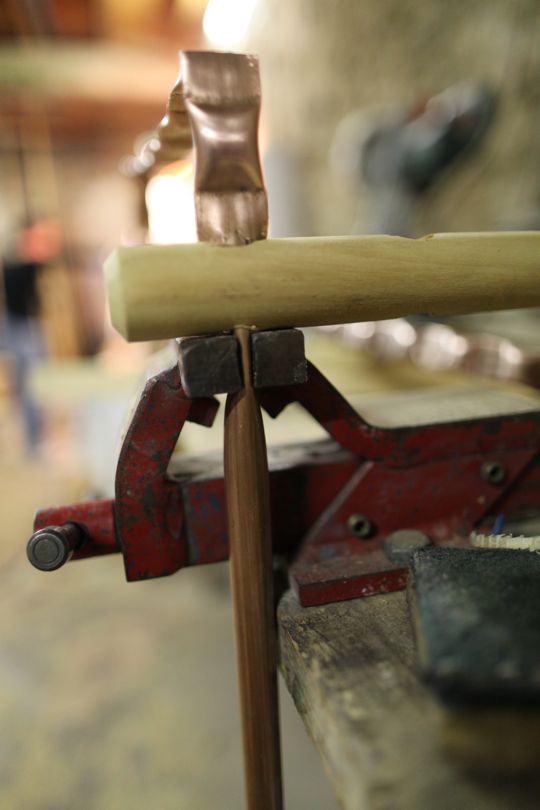
‘After squeezing of the timber cross members against the last copper crimp on each leg segment are completed, the vice completes the final locking crimp that holes the timber tight in place’ – Tomas Kral Boisbuchet – Image Dean Homicki
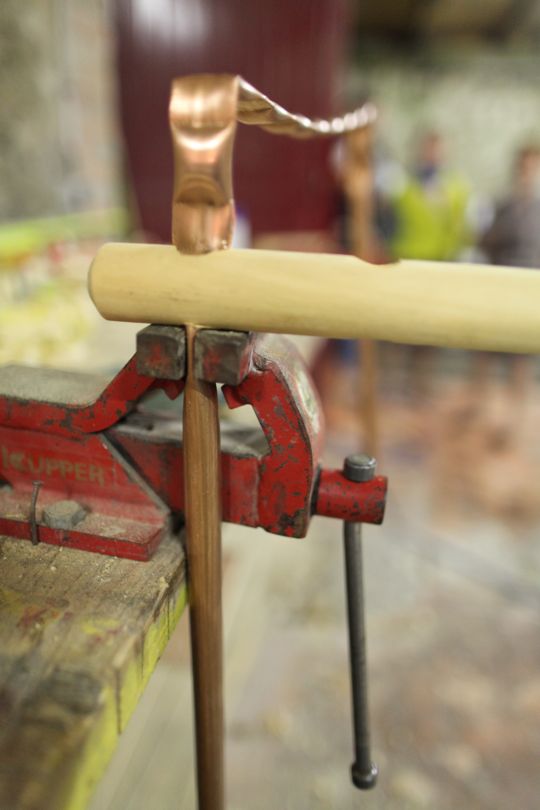
‘The vice completes the final locking crimp that holes the timber tight in place’ – Tomas Kral Boisbuchet – Image Dean Homicki
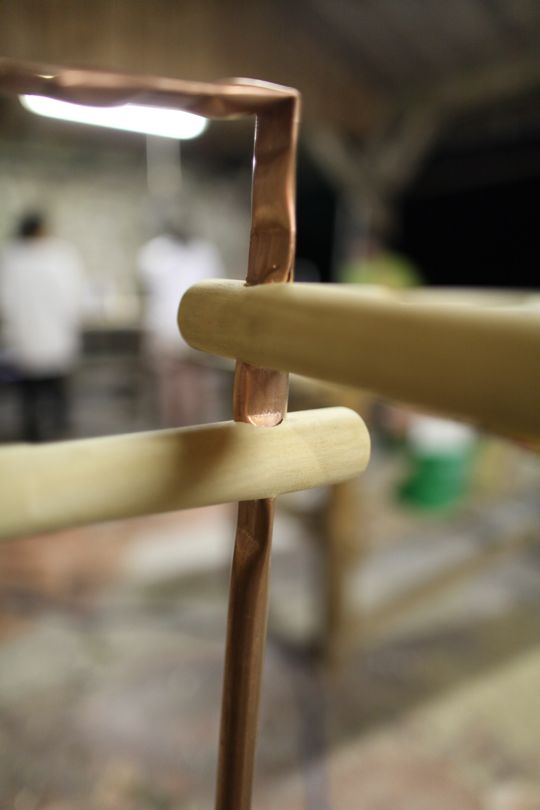
‘Successive crimps made by the vice locking additional timber cross members tight in place’ – Tomas Kral Boisbuchet – Image Dean Homicki
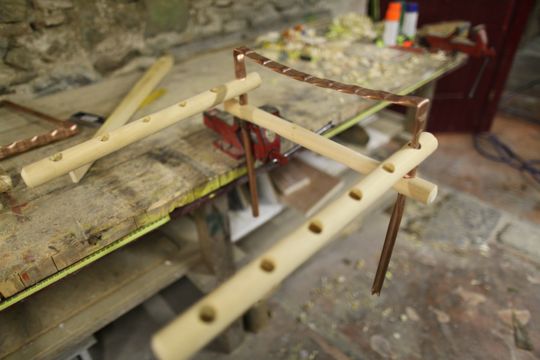
‘The process of assembly. Ready to take the middle copper tube segments’ – Tomas Kral Boisbuchet – Image Dean Homicki
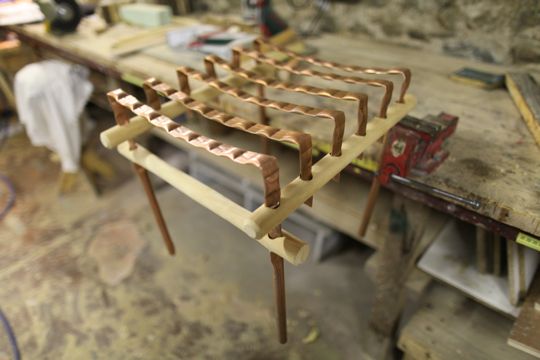
‘All copper tube segments are now inserted in the timber cross members’ – Tomas Kral Boisbuchet – Image Dean Homicki
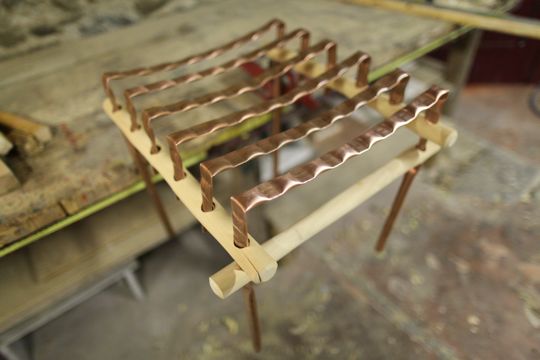
‘Now assembled the stool takes on its own identity born out of the process’ – Tomas Kral Boisbuchet – Image Dean Homicki
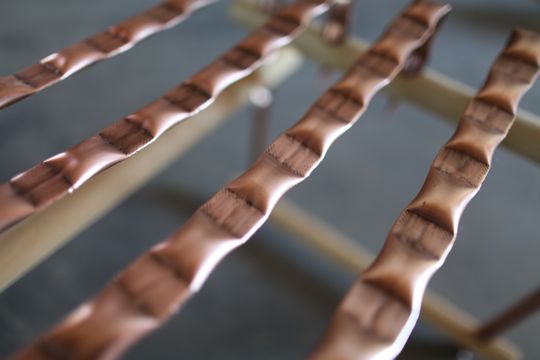
‘A close up of the copper tube bubbles. It now really late so we can make the finishing touches tomorrow. There is always overtime!’ – Tomas Kral Boisbuchet – Image Dean Homicki
This document – ‘DAY 4 – MADE BY PROCESS – DOMAINE de BOISBUCHET France’ is authored by Dean Homicki. It is free to copy, use and alter providing attribution and reference to deanhomicki.com.au is noted. ‘DAY 4 – MADE BY PROCESS – DOMAINE de BOISBUCHET France’ – Dean Homicki – Designer, Entrepreneur, Mentor